Prvním a důležitým upozorněním na začátku bych chtěl řící : Vždy používejte ochranné brýle, i když je laser v nečinnosti nebo procházíte jen kolem (už kvůli odrazům)!!!!
Moje zkušenosti jsou s těmito lasery, vše z čínských obchodů a proto i uvádím jejich výkon v „čínských“ jednotkách, protože nejsem v domácích podmínkách jej změřit. Začínal jsem postupně s těmito výkony 1W, 3.5W, 7W, 15W , 20W , 8W laserem. Od každého výkonu jsem použil i několik variant.
Jak to celé zapojit k 3D tiskárně?
Mám tiskárnu vlastní konstrukce (částečně inspirovanou konstrukcí P3STEEL). Jako ovládací elektroniku mám elektroniku RAMPS 1.4 a ATMEGA256. Zapojil jsem jeden PIN PWM (44) a druhý PIN ENA pro zapnutí (40). Určitě doporučuji PWM zapínat pomocí optočlenu a ENA přes relé, které vypne napájení laser modulu. Ze zkušenosti doporučuji k relé dát sériově ještě klasický vypínač, který, když nebude zapnutý relé nesepne laser (je to taková pojistka proti nechtěnému zapnutí např. při náběhu tiskárny). Celý modul laseru jsem se snažil oddělit od elektroniky tiskárny (tj. má svůj napáječ, optočlen a relé).
Moje 3D tiskárna:
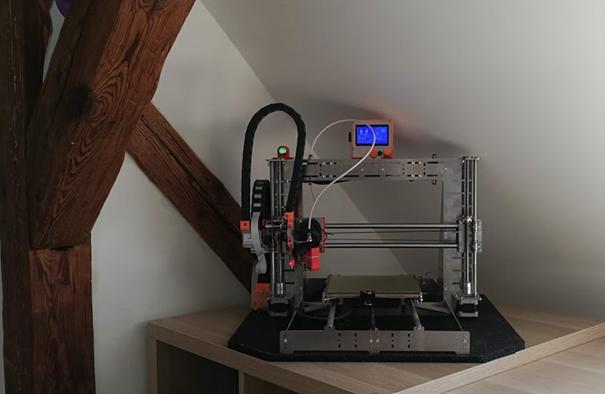
HW příprava :
Každý modul laseru jsem zaměnil za tiskovou hlavu 3D tiskárny. Bohužel co tiskárna tak má jinak uchycení . Já jsem si udělal bajonetové plastové (později) hliníkové uchycení, tj. výměna „nástroje“ byla celkem rychlá. PWM laseru nastavuji od 0(vypnuto) do 255(max).
Zkušenost:
- Nikdy nepouštět modul bez chlazení ventilátoru (laser se přehřeje a odejde)
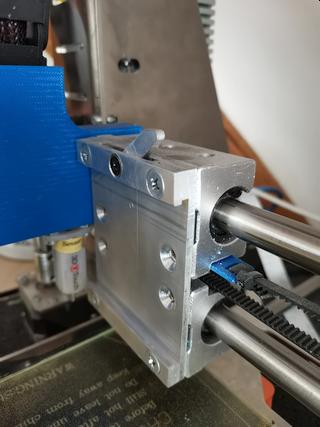
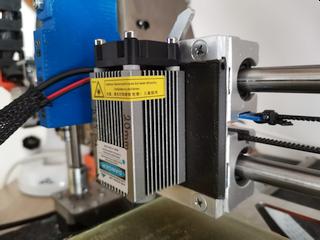
Příprava všeobecná :
Na tiskovou plochu tiskárny vždy pokládám sklolaminátovou desku, aby laser v případě nepropálil tiskovou plochu. Desku sponkami aby se nehnula. Poté si pustím laser (nezapomenout na ochranné brýle) na nejmenší PWM aby jen slabě svítil. Poté pod něj umístím DPS s krycí vrstvou (fotocitlivá fólie, barva …) a pomocí izolepy přilepím ke sklolaminátu. Pokud dělám oboustranné DPS je potřeba ještě deska zrcadla o velikosti tiskové stolku (více vysvětlím níže)
Příklad uchycení :
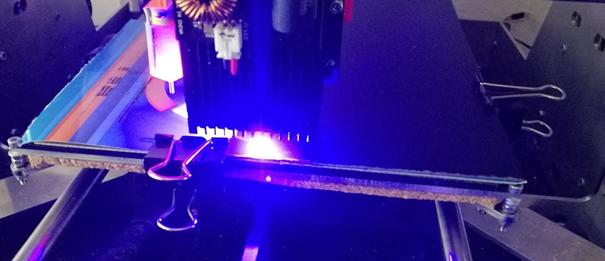
Popíšu zde různé metody, jak jsem je postupně zkoušel a případně k nim mé zkušenosti:
První experiment (používal jsem moduly 1W a 3.5W)
Můj první laser modul byl 1W, a v té době jsem ještě o barvě moc nepřemýšlel, ale napadlo mě použít laminovací fotocitlivou fólii a místo fotocestou to osvítit laserem.
První experiment, podprojekt bitmapa
První co mě napadlo, bylo zkusit použít fotocitlivý DPS (fólie) a po jednotlivých řádcích (něco jako laserová tiskárna) vypálit DPS. V té době ještě neexistoval SW, který by to převedl z bitmapy do G-code tak jsem si rychle něco sepsal. Podle simulace to vypadalo dobře.
Nahrál jsem g-code do tiskárny, dal výkon laseru na hodnotu kolem 30 a testoval.
A zde první pokusy
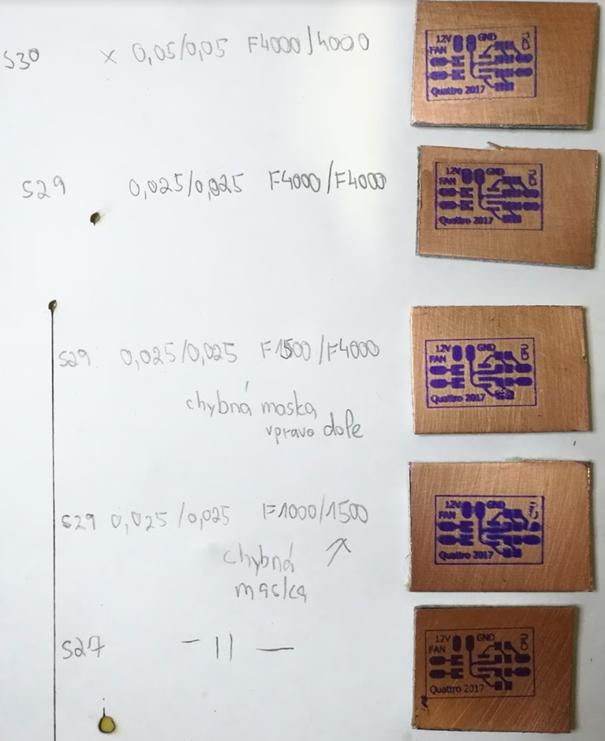
S znamená PWM laseru, 0,025/0,025 rozlišení kroku v mm v ose X/Y a F je rychlost pojezdu svítí/nesvítí. Další zpracování je stejné jako u fotocesty (vývojka, oplach, leptání)
Zkušenosti:
- Setrvačnost laseru při pohybu po X ose je celkem velká, tj. pro pálení je vhodná nižší rychlost.
- Nemá cenu pálit vysokým výkonem, protože se osvítí i část okolo paprsku
- Mám teorii, že při zapnutí / vypnutí modulu (pwm na 0 a pak na hodnotu PWM) laser svítí větší intenzitou a tak kde se zapínal tam je to takové kostrbaté.
Zde pohled na SMD pouzdro
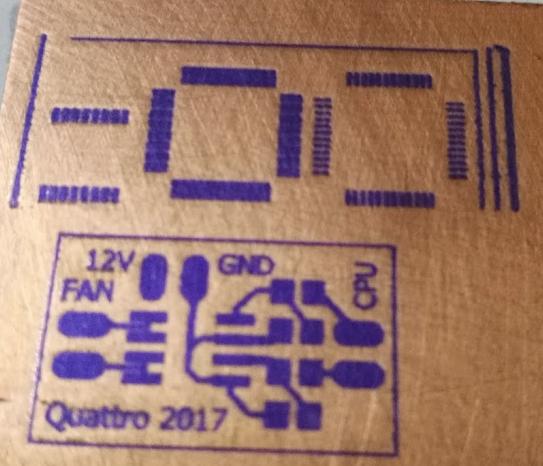
Resume :
Je to asi dobré na DPS pro klasickou montáž (ne SMD) kde budou cesty dál od sebe. Je to pomalé z důvodu řádkování. Pro mě nepoužitelné
První experiment, podprojekt vektory
Popis jak vygenerovat vektorový g-code jsem popsal v prvním článku, jen zde je použito místo barvy fotocitlivý materiál. Zase zde platí pálit slabým paprskem, jezdit pomalu.
Zde je DPS dělán tímto postupem :
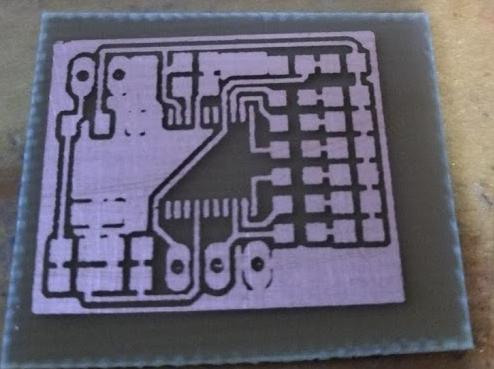
Zkušenost :
- Plastový držák hlavy jsem komplet předělal na hliník a vše dotáhl, aby pojezd byl plynulí
- Přešel jsem na rychlost F400 , která už vyhovovala všem dalším pokusům
- Ještě k laminování, používám neupravenou laminovačku Peach PL703, prošlo tím několik desítek DPS , řekl bych i stovek DPS a drží stále

Resume : toto už je použitelné, ale stejně jde vidět, jak se chvěl laser při pojezdu (chce to pomalejší rychlost)
Druhý experiment – nalezeno na internetu
Nalepit balicí pásku (50mm) a v té vypálit pomocí vektorů cesty. Co se má odleptat tak pomocí skalpelu odstranit . Chtěl jsem to jen zkusit
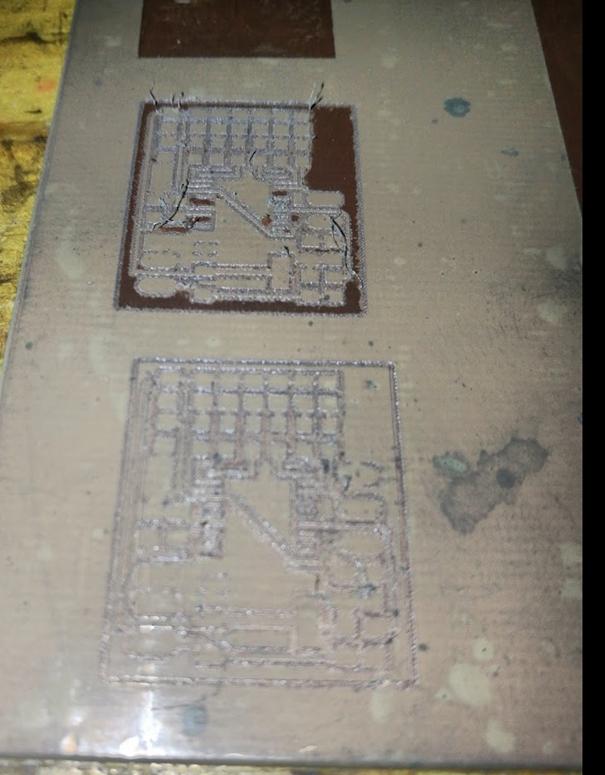
Resume:
- Odlupování na dlouhé zimní večery
- Tam kde projel laser tak to stejně nešlo dolu nebo zbylo lepidlo
- Celé je to kostrbaté
- Nepoužitelné
Třetí experiment – frézování
Koupil jsem v lídlu mikrobrusku s bowdenem tak jsem to chtěl zkusit. Bohužel nejde to upevnit tak aby to fungovalo, více kdyžtak v jiném článku jak jsem přešel na CNC frézku.
Zde je výsledek z frézování pomocí bowdenu
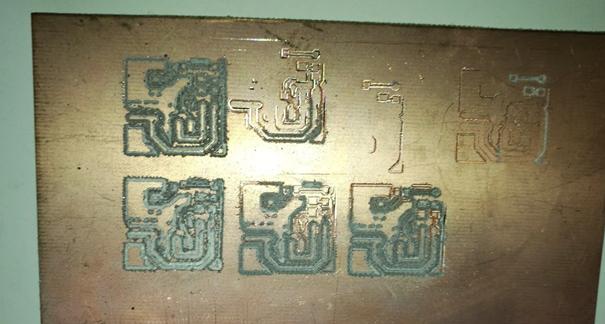
Čtvrtý experiment – klasická černá matná barva
Postup jsem popsal již v prvním článku, takže zde se zaměřím spíše na detaily a co se dá vylepšit.
Ukázka DPS proti světlu po vyleptání
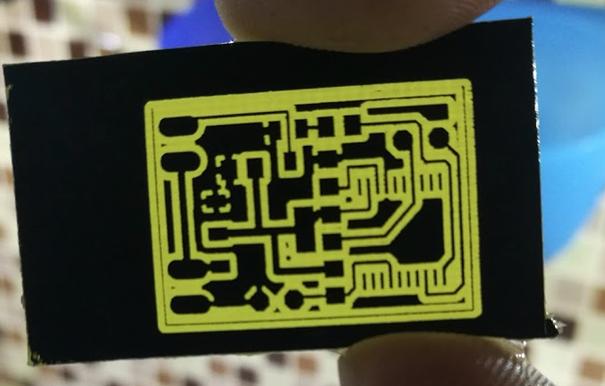
V rychlosti vezmu ještě znovu postup :
Na odmaštění DPS nastříkám v tenké vrstvě matnou černou barvu a nechám pořádně zaschnout. Nesmí nikde být vidět měď. Pokud chci dělat oboustrannou DPS tak si stříknu poté i druhou stranu. Barva je celkem odolná po zaschnutí proti oděru. Pak připevním DPS do tiskárny. Laser nyní je nutné nastavit na skoro max. výkon , pro 7W jsem používal S255, pro 15W cca S200, pojezd F400. V Flatcam jsem nastavil sílu laseru na 0,15mm a dělal jsem vždy minimálně tři průjezdy s překrytím 30%. Až je DPS vypálen, jde již vidět je trošku lesklejší než zbytek barvy. Poté dám oplachování, přejížděl jsem pomocí jemného štětce až se začaly vypálené cesty krásně objevovat. Pak už jen vyleptat.
Fotky jak to vypadá při oplachu
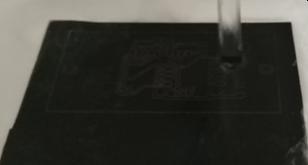
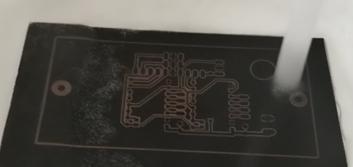
Zde jsem hojně používal 15W laser modul s pevnou čočkou. Bohužel za několik měsíců začal mít problémy a tak jsem hledal příčinu. Našel, byla naprasknutá čočka. Po konzultaci jsem dospěl k názoru, že výpary z barvy se usazují na čočce, která pak není 100% propustná a část paprsku se odráží. Druhý názor je, že se může odrážet paprsek od mědi do čočky. Proto jsem se rozhodl pro dvě úpravy, které asi pomohli, protože laser jede do dnes. První úprava je, naklonění celého modulu laseru tak, aby odražený paprsek se nevracel do čočky, ale dopadl případně na chladič. Druhá úprava byla více foukat z boku aby výpary nestihly doplout k čočce.
Zkušenost :
- laser 1W je nepoužitelný, 3.5W je na hranici, větší výkony jsou OK
- oplach se štětcem jsem zaměnil za CIF krém s mikročásticemi, šlo to mnohem lépe. I když jsem si myslel, že je to OK, je lepší chvilku navíc pokračovat, jinak to má tendenci se odleptat později
- Před leptáním vždy po oplachu zkontrolovat jestli někde nezbyl nějaký mikromůstek
- Změna HW modulu (naklonění kvůli odrazům, a ofuk z boku kvůli výparům)
Fotky náklonu laseru a uchycení
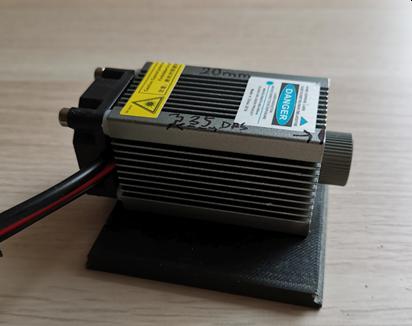
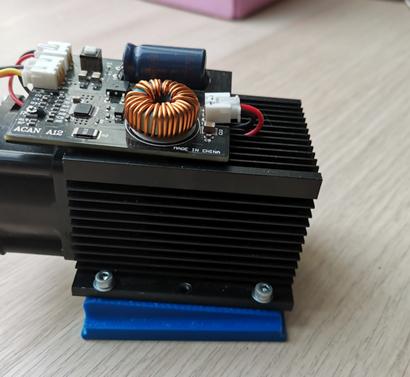
Jak na oboustrannou DPS ?
Ve flatcam posunu DPS tak, aby levý dolní roh byl přesně v souřadnicích 0,0. Nejprve udělám první stranu DPS. Poté si v rozích, kde bude ořez dps vyvrtám díry cca 0,6mm, čím přesněji tím lépe (proto si nechám laserem i udělat kde přesně bude ořez desky). Poté DPS dám do tiskárny, ale podložím jej zrcadlem (aby odráželo směrem k DPS, odrazová plocha je dole). Nyní zapnu laser na minimální výkon a DPS pohybu tak, aby do levé dolní dirky svítil laser. Když bude přesně nad dírou, tak bok zrcadla začne jasně svítit, jak se začne lámat laserový paprsek v zrcadle. Vynuluji souřadnice tiskárny. Přichytím si tento bod, a jdu takto udělat další. (souřadnice znám z Flatcam, pro všechny čtyři rohy). Tento krok chce opakovat několikrát až všechny čtyři rohy „svítí“. DPS je přilepeno k zrcadlu. Pak už se postupuje obdobně jako s první vrstvou. Není to úplně přesné, ale řekl bych, že do tolerance domácí výroby DPS je to postačující.
Pátý experiment : vrtání DPS
Zde to vezmu trošku zrychleně, jde to, ale je to nouzovka. Zkoušel jsem připevnit mikrovrtačku proxxon , je moc těžká, tj. pohyb musel být pomalý, V té době byla akce v lídlu na mikrobrusku s bowdenem. Koupil jsem a zkusil – zde mohu říci, že to funguje.
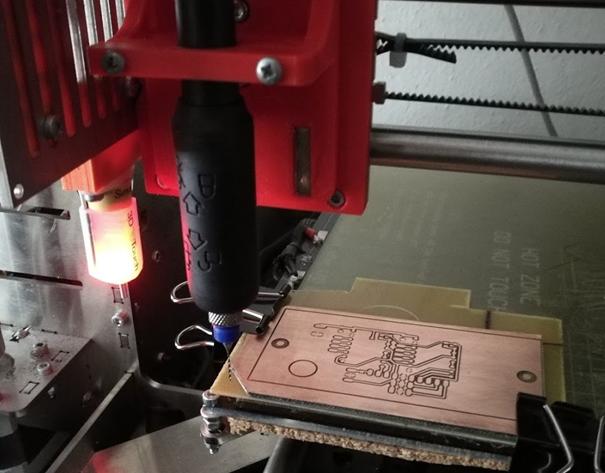
Zkušenost:
- S bowdenem to funguje
- Je z toho „bordel“ tj . po přechodu na 3D tisk, je nutné vše pořádně očistit
- Bowdenové sklíčidlo má mírné vůle
- Pozor na provrtání fólie na 3D tisk, pokud používáte
A co říci na závěr:
Prošel jsem několik etap domácí výroby DPS, od kreslení pomocí per, propisot, úprava plotteru, nažehlování, fotocesta až po laser. Řekl bych, že tato metoda mě nadchla, úspěšnost byla veliká, ale je to spíše na domácí (nesériovou výrobu). Pro výrobu více jak jednoho stejného DPS , si myslím, je lepší fotocesta. Na druhou stranu, s tímto nejsou celkem žádné starosti, hlídat čas osvitu, různé vyvolávání atd.. Prostě dá se DPS , pustí tiskárna a za pár desítek minut se přijde a DPS je celkem obstojně nakreslen. Ještě jsem se nevyjádřil k času. Záleží dost na velikosti DPS, ale většinou jsem se pohyboval v desítkách minut. Ideální laser modul považuji ten 8W, protože je celkem lehký a dostačuje pro tuto práci. Určitě dodržovat ohniskovou vzdálenost aby laser byl zaostřen, když se např. dělá oboustranná DPS a použije se zrcadlo, musí se posunout o výšku zrcadla nahoru osa Z. Prošlo mi rukama několik laserových modulů bohužel některé měly paprsek ne kruhový spíše bych řekl obdélník. S těmi pak nejde, nebo hůře jde dělat DPS, protože v jedné ose bere 0.1mm a v druhé např. 0,15mm. Bohužel při objednávce modulu Vám toto prodejce neřekne…. Tento postup výroby DPS jsem používal většinou pro SMD DPS, kde nejmenší cesta a mezera byla 0,016 palce cca 0.4mm co bylo menší už byl celkem problém. Používal jsem např. pro ATMEGA256, STM32F103, ATMEGA v SMD, RCL ve velikosti 0805 a 0603 a vše funguje v pohodě.
Předminulý rok, jsem si řekl, že nebudu již moc špinit 3D tiskárnu, a tak jsem se rozhodl postavit nebo koupit malou frézku na DPS a případně na nějakou tu modelařinu (balzu, papír). Nakonec to dopadlo trošku jinak a přešel jsem na CNC frézování DPS, které bych řekl, že je pro mé účely o řád lepší jak pomocí laseru, ale k tomu kdyžtak v jiném článku.
A tady pár fotek DPS , dělané pomocí laseru a barvy
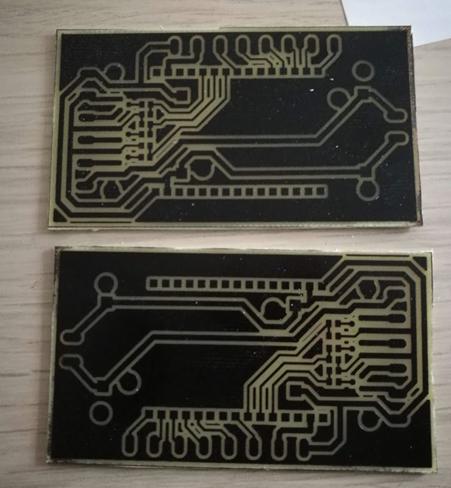

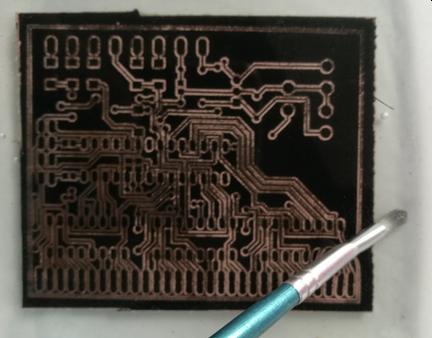
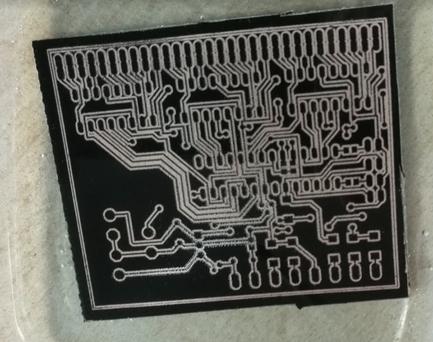
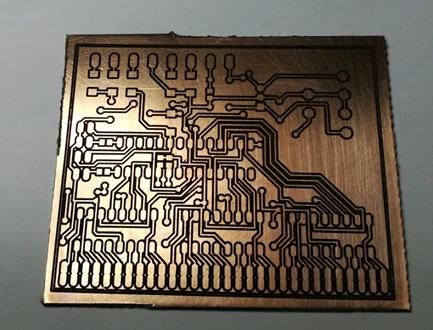